Nearly all electric vehicle (EV) projects share the same weakness: the vehicles become obsolete or lose market-leading position quickly as new batteries are released every few years in the same model. Having accrued more than a decade of experience working on large-scale EV projects at Tesla and Xing Mobility, the Graft team has chosen to design our own battery format as a way of ensuring that customers are guaranteed at least a decade of reliability, with the expectation that we also have the capability to design for both forward and backward compatibility. This article takes an in-depth look at the ethical, technical, and material decisions that shape our batteries.
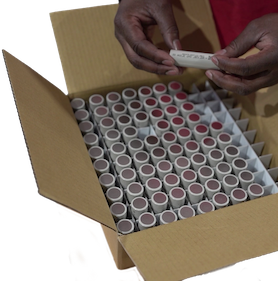
From Planned Obsolescence to Sustainability
When there’s no upgrade plan for the power source of electric vehicles, the vehicles lose considerable value as they age and their range and power output decline. Unfortunately, this situation has affected smaller EV companies and large alike, with well-known models like the Nissan Leaf and even early Tesla cars suffering from battery degradation and loss of power. It wasn’t lost on these companies – and it’s not lost on us – that vehicles are designed to last a very long time, with the motor, motor controllers, and several other components easily lasting 10 or even 20 years. But due to changing technology, battery packs are the most likely culprit to make EVs obsolete. We want to be able to offer our customers an upgrade path, whether that's with solid state batteries, lithium ion batteries, or whatever is coming in the future, we guarantee our customers will access that technology in our swap format.
In pursuit of our ten-year guarantee, our electronic package is designed to be flexible and upgradeable. This commitment is a key to extending the service life of our vehicles and creating more value for riders. While battery cell formats and chemistries are sure to evolve over time, our battery swap system will be able to utilize the latest technology available for our complete range of vehicles, new and old. In the future someone could buy one of our vehicles that is ten years old and has had a very rough life, then buy a brand new battery and the range would be double what that vehicle had when it was new. Conversely, if you have a new vehicle and you want to buy a used battery, that would work, too, creating forward and backwards compatibility and sustaining the value of the used batteries.
Swapping across our product line is another value add, and another area in which Graft is the only EV brand to offer this feature. Of course, swappable batteries offer the advantage of going on longer rides. But for owners of multiple vehicles, this creates an added layer of convenience, so that a family might share batteries between a buggy and two motorcycles, or an ATV tour company might swap batteries between ATVs and buggies. Alternately, batteries may be swapped between summer and winter vehicles, significantly reducing costs for owners. Far too often devices that work perfectly well become obsolete when the battery starts to fade and there’s no cost-efficient way to replace it, but Graft products retain their utility and value because we make battery upgrades easy.
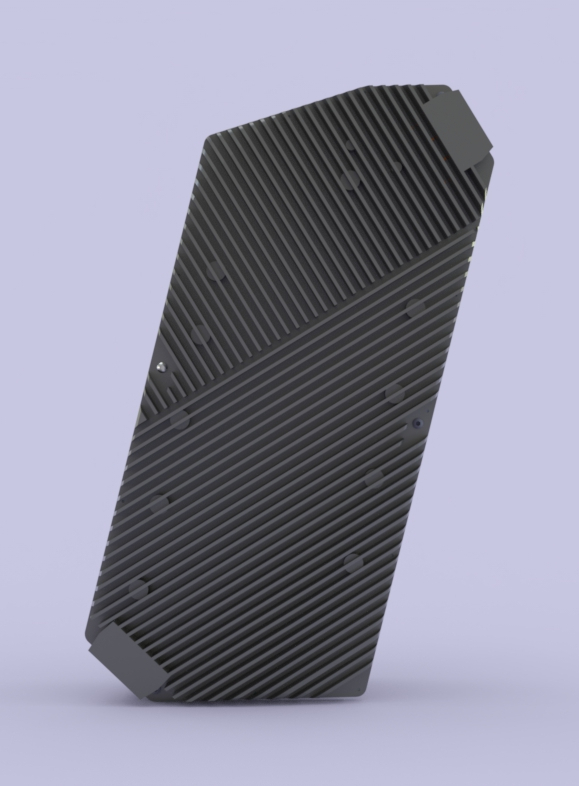
Swappable vs. Exchangeable Batteries
We're the only company in the market offering swappable batteries. Our batteries are truly swappable, not just exchangeable. The difference is that they're designed to be swapped many thousands of times. The swap is an engineering process that is accommodated for and expected within the normal life of a battery. Some electric vehicles have exchangeable batteries where the connectors have around 50 cycle ratings. After you've latched 50 times, you reduce the performance and the connector needs to be replaced.
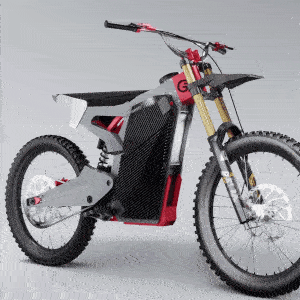
Our swap system uses a blind mate system, meaning the user can just push the battery in and the electrical connections happen automatically. We have safety systems in place that connect before engaging high power. When you disconnect, those safety systems disconnect the power first to eliminate sparking, short circuits or arcing during the swap process.
To illustrate an example of arcing, many exchangeable EV batteries don’t have a safety system designed to make the batteries exchangeable. They're exchangeable from an assembly process at the factory, but if the user were to disconnect the battery while still under high voltage they would get a big spark. Doing this just a handful of times will damage the connectors.
Graft Battery Technology
Thanks to our considerable experience with battery technology, at Graft we purchase cells, fuses and relay, and we manufacture the remaining components in house to our specifications.
Our cells are 21700 lithium ion cylindrical batteries, a type commonly used in Tesla vehicles and some of the latest electric vehicles. Our batteries are designed for very high power and very long cycle life. These premium battery cells are supplied by Molicel, a Taiwanese partner that we have a long working relationship with.
With these cells, we manufacture our own battery management system (BMS) in house. A BMS is an electronic system that monitors battery cells for safety. The system checks on the battery thousands of times per second to see that each and every cell is at a safe operating voltage and temperature.
For assembly, we insist on laser welding and we don't use any wire bonds. Wire bonding is a process that Tesla has made quite famous, but it has led to some failures in applications with high vibration. Resistance welding is the cheapest, most common process but it introduces a lot of heat into the battery cells, which can damage the cells’ long-term stability. In addition, resistance welding is not a stable welding process and requires replacement of weld electrodes which wear with every weld. This leads to inconsistent weld quality.
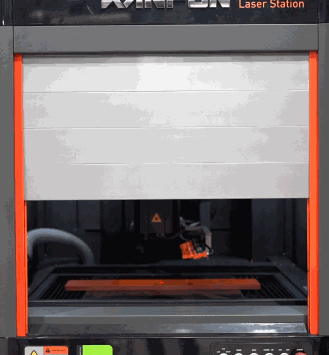
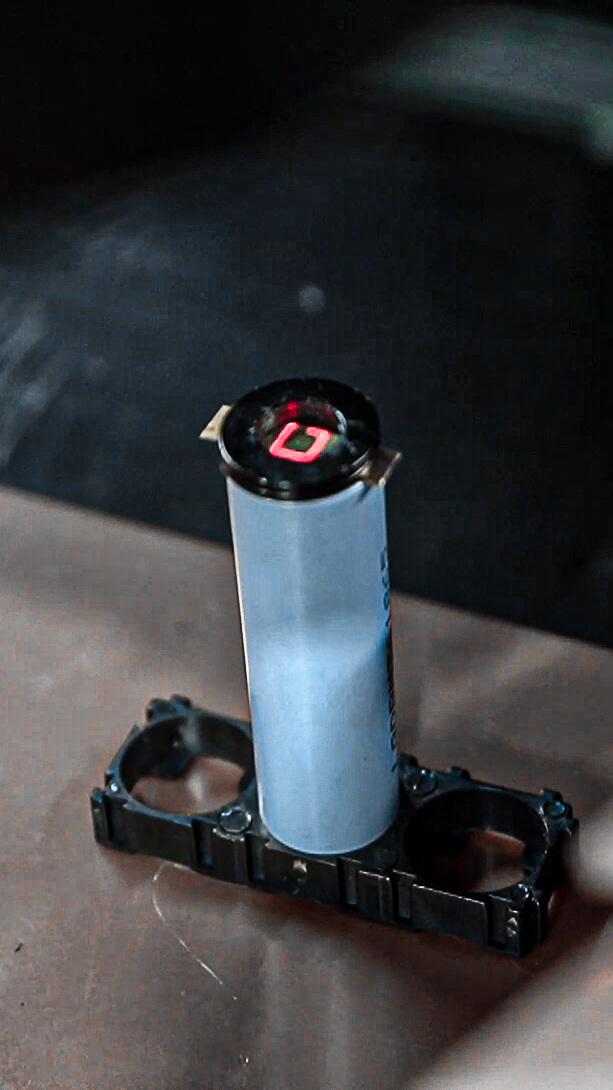
Also, most batteries use nickel to transfer electricity from cell to cell because it is easy to weld even though it is not a great conductor. Laser welding is the only process in which copper can be directly welded to the steel. So we choose to use the costliest welding process because using copper for better conductivity and reducing the heat inside the battery increase efficiency. Similarly, we don’t compromise on quality when choosing smaller, but still essential components. For example, we use Raychem Spec 55 wire, which was originally designed for spaceships and came from Azizi’s time in NASA. This wiring cable costs three or four times as much as other cable but it greatly outperforms regular cable in terms of safety because it’s almost fireproof and can handle much higher power. Seemingly minor choices to use premium components throughout the build means we end up with a much higher quality product.
Temperature management is essential to vehicle performance and battery life. To handle this, we do direct thermal bonding, meaning that every cell is thermally bonded to a heatsink and has the same surface contact so that each cell has equal access to cooling. This ensures that out of the hundreds of cells that make up our battery, there won’t be hotspots, meaning that the cells will retain their energy and the cells will age evenly.
When we studied our competitors’ packs, we frequently saw that cells in the middle tended to overheat or cells in the corners had no way to let heat off the battery. Doing direct thermal bonding means we're able to keep the cells cooler, which means longer life, which means longer and better return on investment for our customers. We guarantee 2,500 charge cycles, while many of our competitors struggle to get 200 charge cycles.
Our aerospace-grade aluminium heatsink thermally bonded to the batteries is unique in the market and it is crucial to ensure our industry-leading cycle life. The heatsink also provides critical protection - the fins on the battery heatsink are designed to bend in case of a severe accident and that absorbs energy and keeps the impact from damaging the battery. It's also an indicator to the customer on how much damage the battery has gotten. If the fins are bent, no problem. But if there is a bend in the actual base plate, the battery must be inspected by Graft or a dealer.
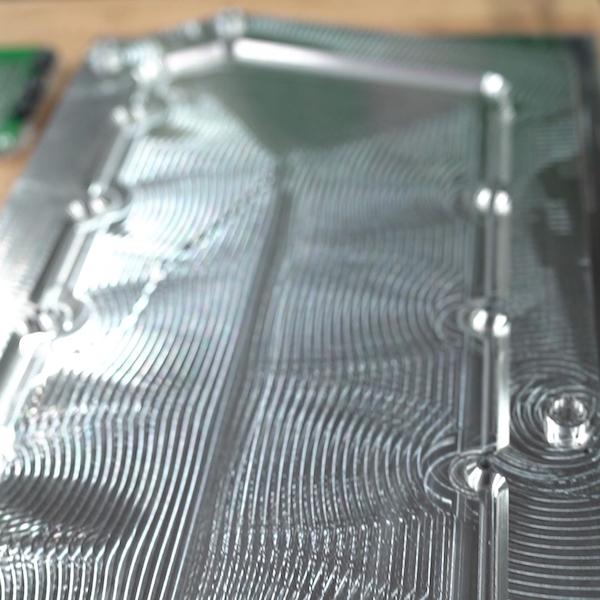
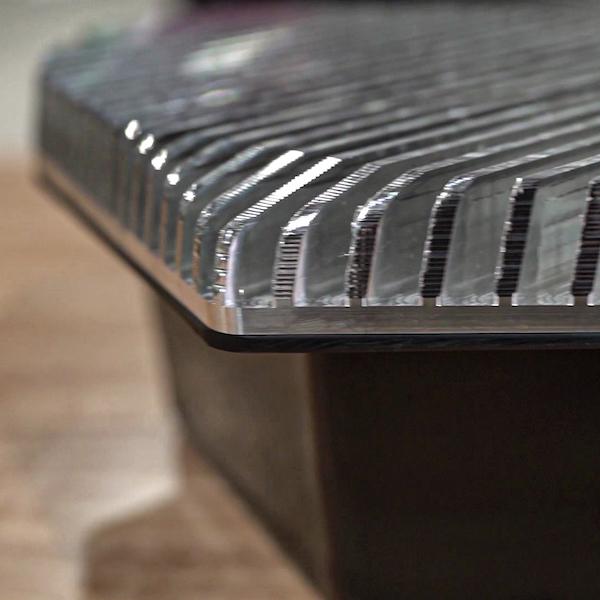
The battery heatsink is designed as a stressed member. It increases the stiffness and strength of the vehicles’ frames. The final thing to note about the battery is our fast swap system, which uses a special tool and aircraft-grade fasteners which are designed for a thousand cycles, another premium detail that contributes to a safe, secure riding experience. Battery swaps can be completed in less than 60 seconds, faster than refilling a gas vehicle.
Safety, Flexibility, Capabilities
The decision to assemble our own batteries comes from a commitment to safety, a desire for flexibility and control over the assembly process, and an understanding of what technical capabilities we possess. Our team’s experience managing quality control for battery manufacturing came with an understanding that the risk of battery fires is so severe that you owning the QC empowers you to make decisions you believe in, in terms of safety and quality.
The key safety elements are the cells, the BMS, the design, and the assembly process. We build, test, and monitor every single battery pack and – with the exception of the battery cells - we manufacture virtually everything in house. We understand each battery, serialize every battery, and record the test results from every battery pack into our manufacturing database so every battery pack is well known and understood from our side.
We own our BMS manufacturing by leveraging our parent company, Vanda Electronics, which creates motor controllers, wire harnesses, printed circuit boards, and electronics. One of the main advantages here is flexibility and the ability to monitor processes exactly for the product at hand. We are able to design very closely, with the people who are making the printed circuit board, we have day-to-day conversations, and we're onsite quite often. So we have a deep understanding of the capabilities and limitations of the equipment, which means we'll get a higher quality circuit board than someone who's ordering the circuit board from a company halfway around the world. To add to that, we are able to do panelization and some of the more advanced circuit board processes with a higher level of technical competence than would typically be possible.
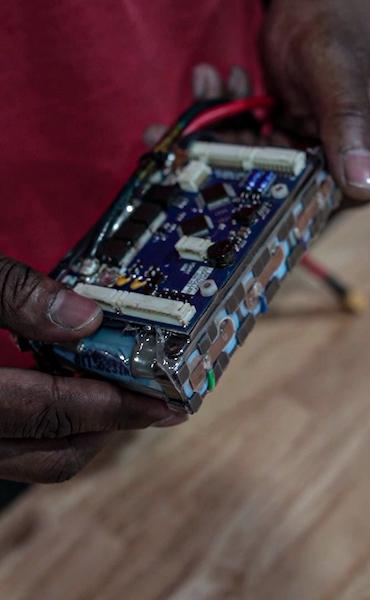
How the Battery Supports Your Ride
The battery impacts the ride most directly through the use of power modes and our vehicles’ climbing ability. Our motorbike has three power settings, and our ATV will have two. Because the vehicles are so powerful, quite often you don't need all of the power and you may want to make it a little easier to manage in slippery conditions or for an absolute beginner. Riders can switch between modes on the fly with a button on the handlebars. The lowest mode will provide the longest range, whereas the higher modes offer greater top speeds for more aggressive riding, but shorter battery life.
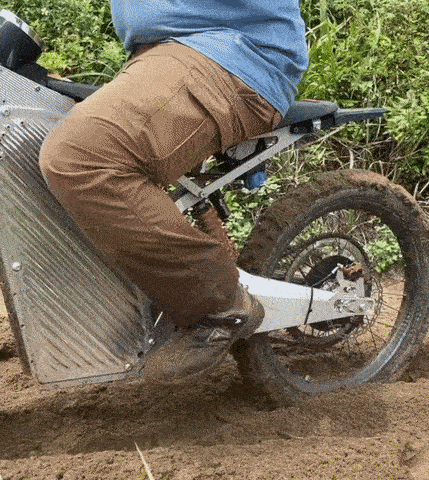
We are very proud of the power of our vehicles. For the motorbike, we've matched the battery performance, frame performance, the motor and controller performance to a 300 CC motocross bike. So climbing a flight of stairs is no problem, climbing inclines you couldn’t walk up or down, this bike can climb.
People who want performance like this on competing bikes are doing all kinds of upgrades, replacing tires, brakes, handlebars, battery, motor controller, rear wheel, seat and bodywork which means you're only keeping the frame. But then you have a frame that was designed for much lower power than what you're putting in.
Power for the People
At the end of the day, we build our batteries because they are an integral part of the riding experience and vehicle value, which are our customers’ primary concerns. We want these machines to be ridden for fun and function for a decade and more, so we build them to last, from the power supply to the bar ends and fenders. Stay tuned for our next post, in which we will break down how riders can level up their skills from beginners to very serious trail enthusiasts on our motorbike, without needing to change bikes to keep up with skills growth and the need for speed.